Have you ever stopped to think about how those huge metal boxes that ship goods around the world are made? Shipping containers might look simple, but there’s a lot more going on behind the scenes. Let’s explore the fascinating process of how these containers are created, from the materials used to the design features that make them so durable and reliable for transporting goods across vast distances.
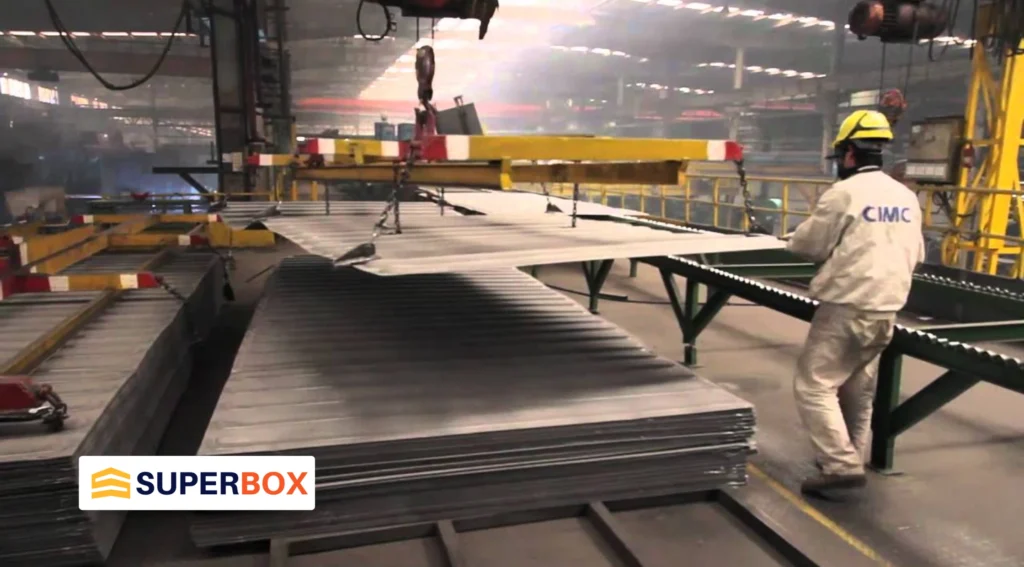
Steel Production: Crafting the Backbone of Containers
The journey of shipping container manufacturing starts with creating high-strength weathering steel, which is essential for the container’s durability and longevity. Here’s how it all begins:
- Starting with Iron Ore: The process kicks off with iron ore, which is a raw material found in the earth. This ore is mixed with coke (a type of coal) and heated in a blast furnace. The intense heat melts the iron ore, turning it into molten iron. This molten iron is the foundation upon which the entire shipping container construction is built.
- Turning Iron into Steel: The molten iron is then transformed into steel. This is done by removing impurities and adding elements like chromium and nickel. These additions make the steel stronger and more resistant to corrosion, which is crucial for containers that will face harsh weather conditions during transport.
- Cooling and Rolling: After the corten steel is created, it is cooled and rolled into thin, flat sheets. These sheets need to be incredibly strong because they’re going to form the wall panels and roof of the shipping container. The cooling and rolling process ensures that the steel is just right for withstanding the tough conditions of global shipping. The sheets are carefully monitored to ensure they meet the required specifications for strength and flexibility.
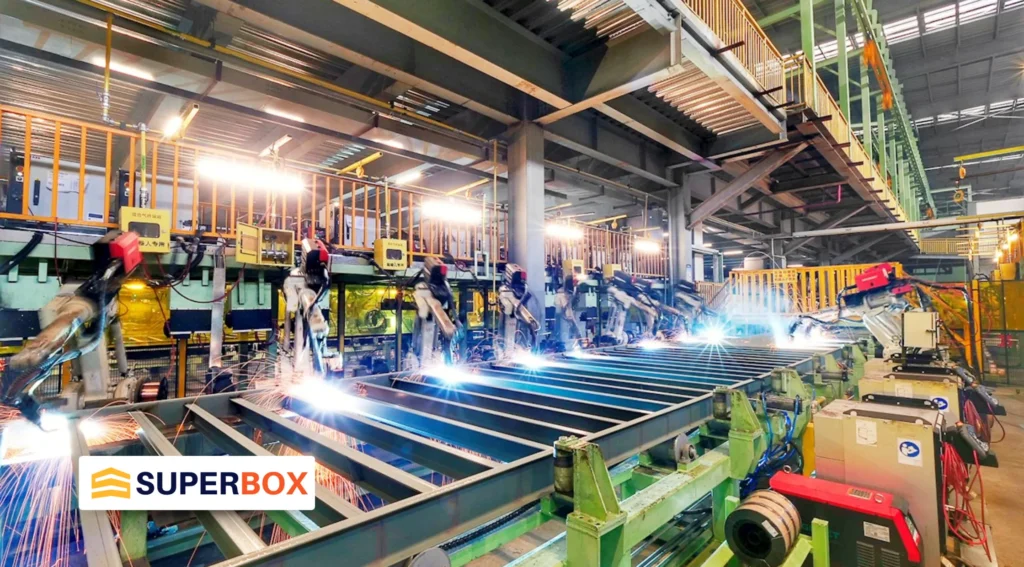
Corrugated Steel Panels: Adding Strength and Flexibility
Once the steel sheets are ready, they’re transformed into corrugated steel panels. This is where the steel gets its unique strength and flexibility:
- Shaping the Steel: The steel sheets are fed through machines that create wavy patterns. This process is called corrugation. The wavy design isn’t just for looks—it makes the steel panels much stronger and more flexible. This is important because the panels need to support heavy loads without bending or breaking during transport.
- Building the Container: These corrugated panels are used to build the walls and roof of the shipping container. The design helps the container handle heavy cargo and shields the contents from weather and other potential damage. It’s a smart design that makes the container both strong and reliable. The corrugated structure also helps distribute the weight of the cargo evenly, reducing the risk of structural failure.
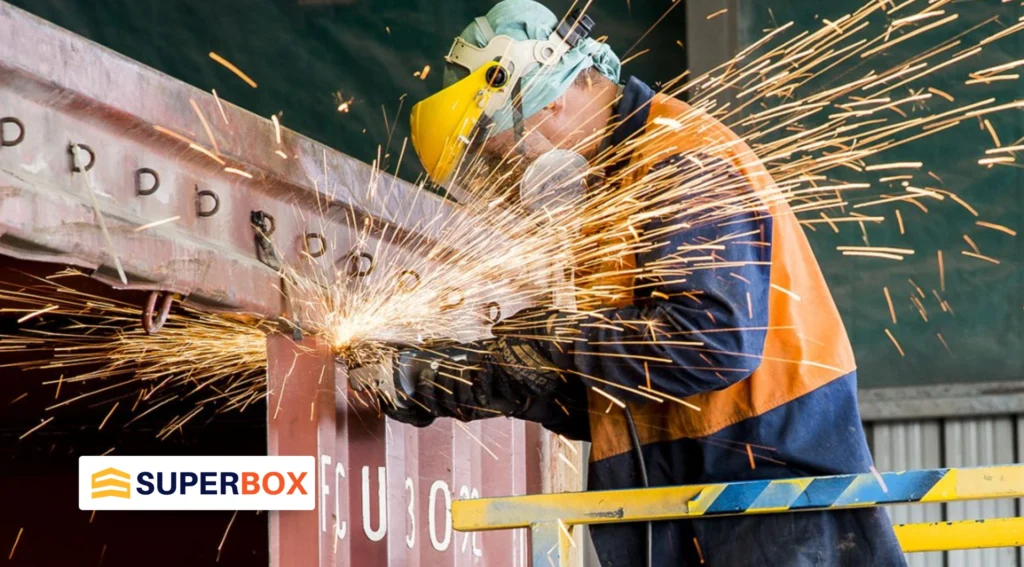
Doors and Hatches: Making Access Easy and Secure
Shipping containers need doors and hatches that are both tough and functional. These components are crucial for ensuring that the contents of the container can be accessed easily while also providing security against theft and damage.
- Designing the Doors: The doors of a shipping container are typically made from the same high-strength steel as the rest of the container. They are designed to swing open easily, allowing for quick loading and unloading of goods. The hinges are robust and designed to withstand the wear and tear of frequent use. Additionally, the doors are equipped with locking mechanisms that ensure the contents remain secure during transport.
- Hatches for Ventilation: Some shipping containers also feature hatches that allow for ventilation. This is particularly important for containers carrying perishable goods that need airflow to prevent spoilage. The hatches are strategically placed to ensure that air can circulate without compromising the container’s structural integrity.
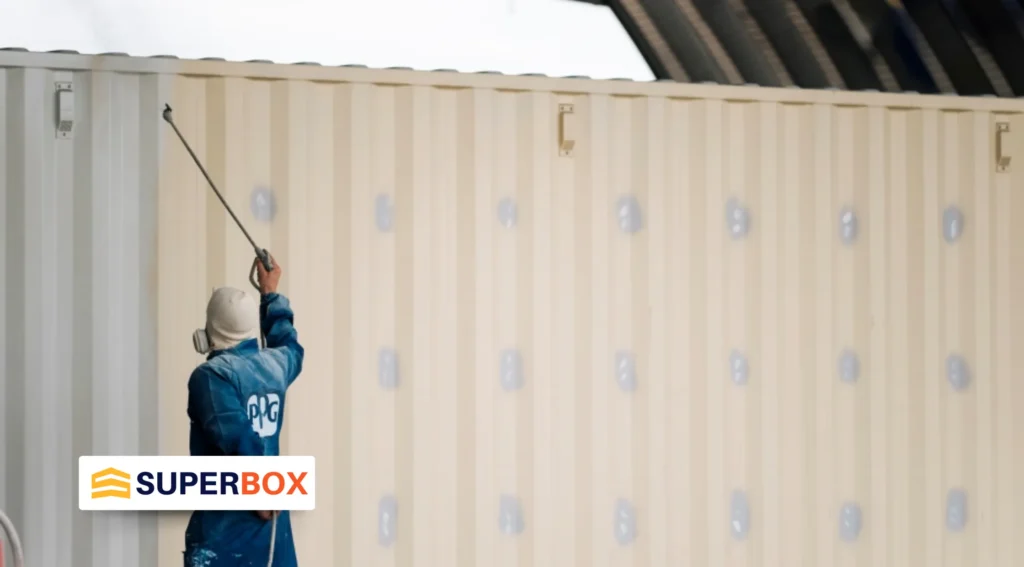
Protective Coatings: Shielding Against the Elements
Once the shipping container is assembled, it undergoes a process of coating to protect it from the elements. This step is vital for ensuring the longevity of the container, especially since it will be exposed to various weather conditions during its travels.
- Applying Primer: The first step in the coating process is applying a primer. This primer helps the paint adhere better to the steel surface and provides an additional layer of protection against rust and corrosion. The primer is carefully applied to ensure complete coverage, especially in areas that may be more prone to wear.
- Painting the Container: After the primer has dried, the container is painted with a high-quality, weather-resistant paint. This paint not only adds aesthetic appeal but also serves as a barrier against moisture, UV rays, and other environmental factors that could damage the steel. The color of the paint can also be chosen based on the shipping company’s branding or specific requirements for visibility.
- Final Inspection: Once the protective coatings are applied, the container undergoes a final inspection. This inspection ensures that all components are functioning correctly and that the coatings have been applied evenly. Any imperfections are addressed before the container is sent out for use.
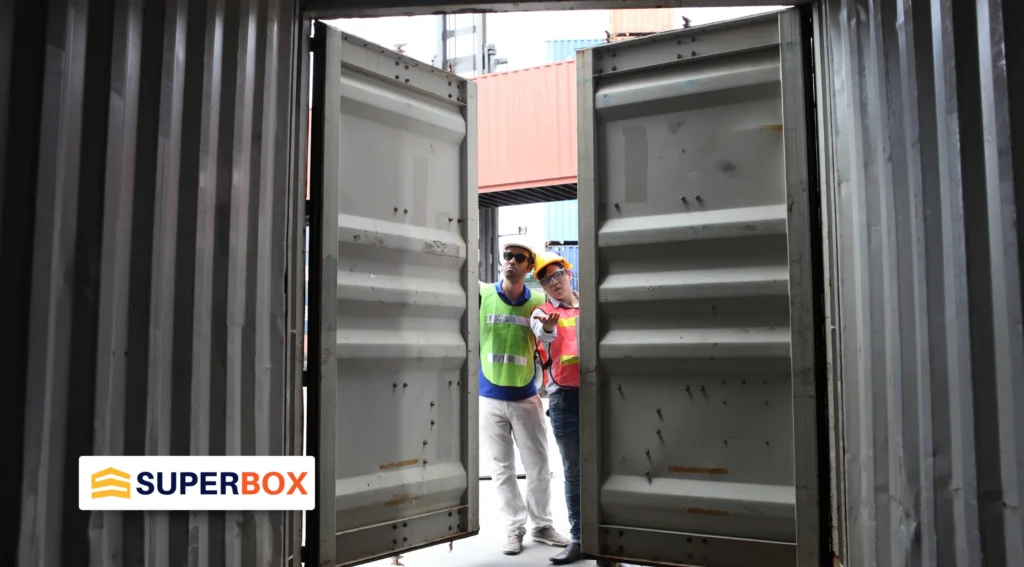
Quality Control: Ensuring Durability and Safety
Throughout the entire process of how shipping containers are built, quality control is paramount. Manufacturers implement strict quality assurance measures to ensure that every container meets industry standards for safety and durability.
- Testing the Steel: Before the steel is even shaped into panels, it undergoes rigorous testing to ensure it meets the required strength specifications. This testing includes checking for tensile strength, ductility, and corrosion resistance. Only steel that passes these tests is used in the construction of shipping containers.
- Final Container Testing: After the containers are fully assembled, they are subjected to various tests to ensure they can withstand the rigors of shipping. This includes pressure tests, load tests, and inspections for any potential weaknesses. Containers that do not meet the standards are either repaired or recycled, ensuring that only the best containers are put into service.
Conclusion
In conclusion, building a shipping container is a complex and fascinating journey that involves multiple steps, from steel production to protective coatings. Each stage is crucial in ensuring that the final product is strong, durable, and capable of withstanding the challenges of global shipping.
Understanding this process not only highlights the engineering behind these metal boxes but also emphasizes their importance in facilitating international trade and commerce. Shipping containers are more than just simple metal boxes; they are a vital part of the global economy, transporting goods and materials across oceans and continents.
Need reliable shipping containers? SuperBox is the answer!
Tired of shipping problems? SuperBox has the answer! We offer strong and reliable shipping containers to keep your cargo safe, no matter how big or small your business is.
Our containers are built tough to protect your goods during shipping. With a focus on quality and durability, SuperBox ensures that every container is designed to meet the demands of modern shipping.
Choose SuperBox for worry-free shipping. Call us today at 1-866-696-9269 to learn more about our offerings and how we can help you with your shipping needs. Our team is ready to assist you in finding the perfect container solution for your business, ensuring that your goods are transported safely and efficiently.