Shipping containers are essential for transporting goods worldwide, and understanding their manufacturing process reveals why they are so reliable. This blog will walk you through the entire shipping container manufacturing process, from assembling components to the final quality checks, making it easy for anyone to understand.
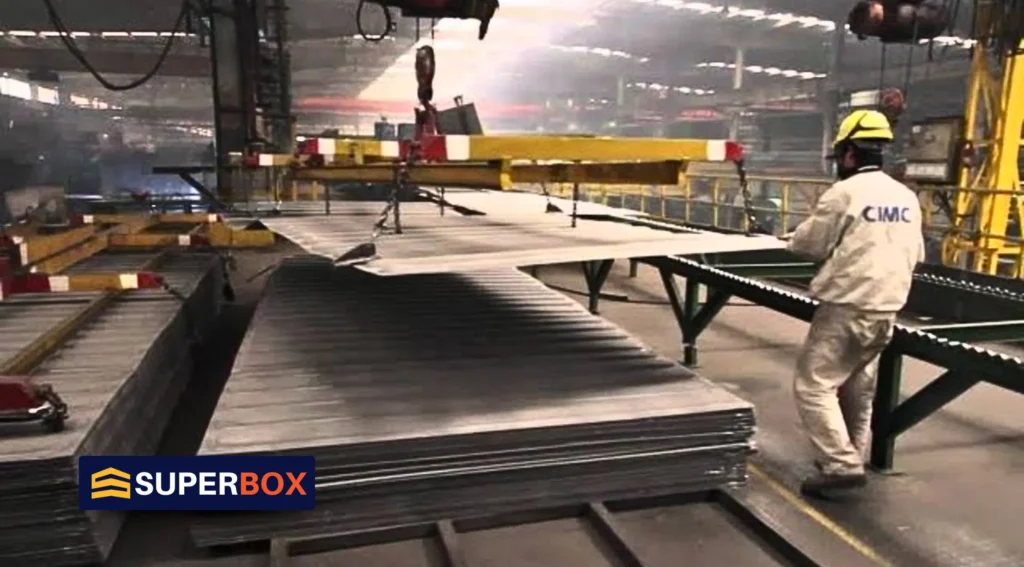
Container Assembly: Step-by-Step Guide to Building a Container
The assembly of a shipping container begins with raw materials, primarily steel. The process kicks off by cutting large steel sheets into panels, which form the sides, roof, and floor of the container. Here’s a step-by-step guide to the assembly process:
- Cutting Steel Sheets: Large steel sheets are cut into panels to create the sides, roof, and floor.
- Corrugation: The steel panels are shaped into corrugated forms, providing strength and durability.
- Welding Panels Together: The floor panel is laid down first, followed by the sidewalls, and then the roof panel. Each part is welded together to form the container’s structure.
- Adding Door Frames and Corner Posts: Door frames and corner posts are welded in place for added stability and functionality.
- Installing the Floor: The floor is made of marine-grade plywood, which is bolted or screwed into the steel cross members underneath the container.
- Installing the Doors: The doors, complete with locking mechanisms, are installed to secure the container’s cargo.
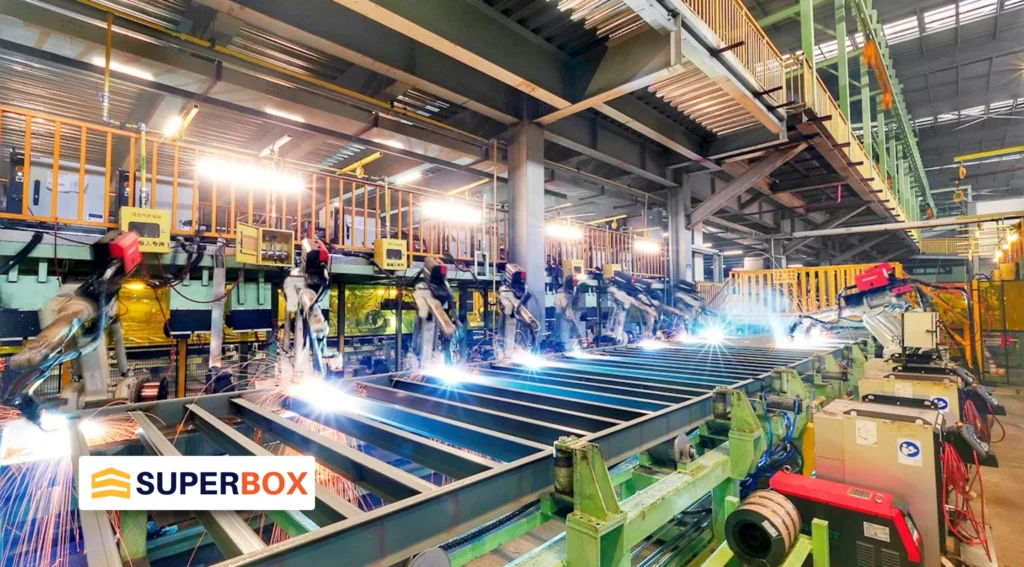
Welding Techniques: How Shipping Containers Are Welded Together
Welding is a crucial part of the shipping container manufacturing process. Here are the key welding techniques used:
- MIG Welding (Metal Inert Gas):
- Process: A continuous wire electrode is fed through a welding gun and melts upon contact with the steel surfaces.
- Result: The molten metal cools and solidifies, creating a strong bond between the panels.
- Application: This method is commonly used for its speed and efficiency.
- TIG Welding (Tungsten Inert Gas):
- Process: A non-consumable tungsten electrode generates the arc, while a separate filler rod is used to join the metal pieces.
- Result: TIG welding provides greater control, resulting in cleaner and stronger welds.
- Application: This technique is used for finer details or when working with thinner materials.
Both welding techniques are essential for ensuring the container’s structural integrity, making it capable of withstanding the harsh conditions it may encounter during transportation.
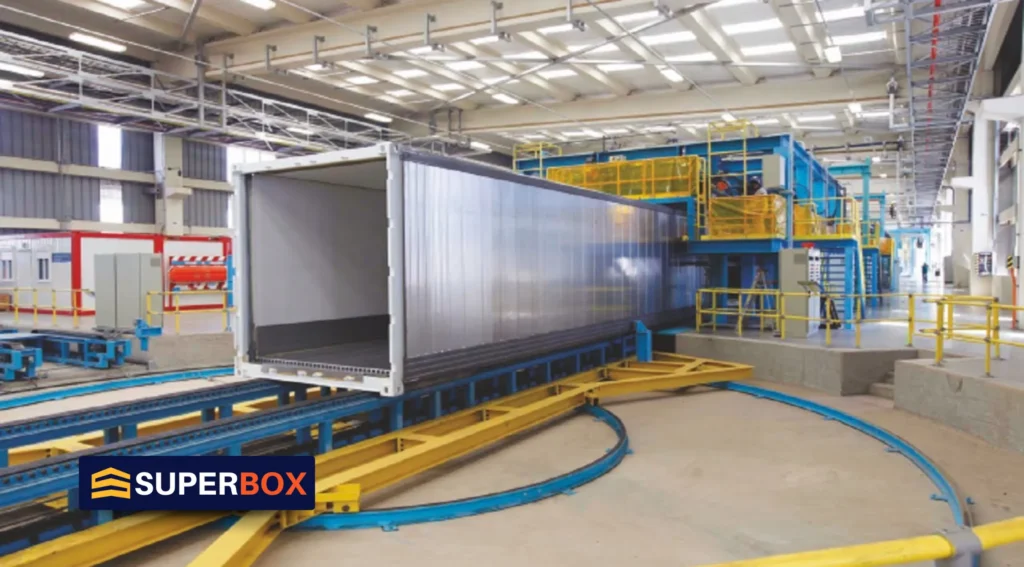
Quality Control Measures: Ensuring the Container Meets Standards
Quality control is a critical part of the manufacturing process for shipping containers. Throughout the production process, various inspections are conducted to ensure the container meets international standards, such as those set by the International Organization for Standardization (ISO).
The first step in quality control is inspecting the raw materials. Steel sheets and other components are checked for any defects that could affect the container’s strength or durability. During the assembly process, each weld is inspected to ensure it is free from cracks or imperfections that could compromise the container’s integrity.
After the container is fully assembled, it undergoes a series of tests to ensure it can withstand the rigors of transportation. These tests include checking the container’s dimensions, ensuring the doors open and close properly, and conducting a watertightness test. In this test, the container is sprayed with water to ensure no leaks are present.
Any issues found during these inspections are addressed before the container is approved for use. This rigorous quality control process ensures that every shipping container is built to last and meets the high standards required for global transportation.
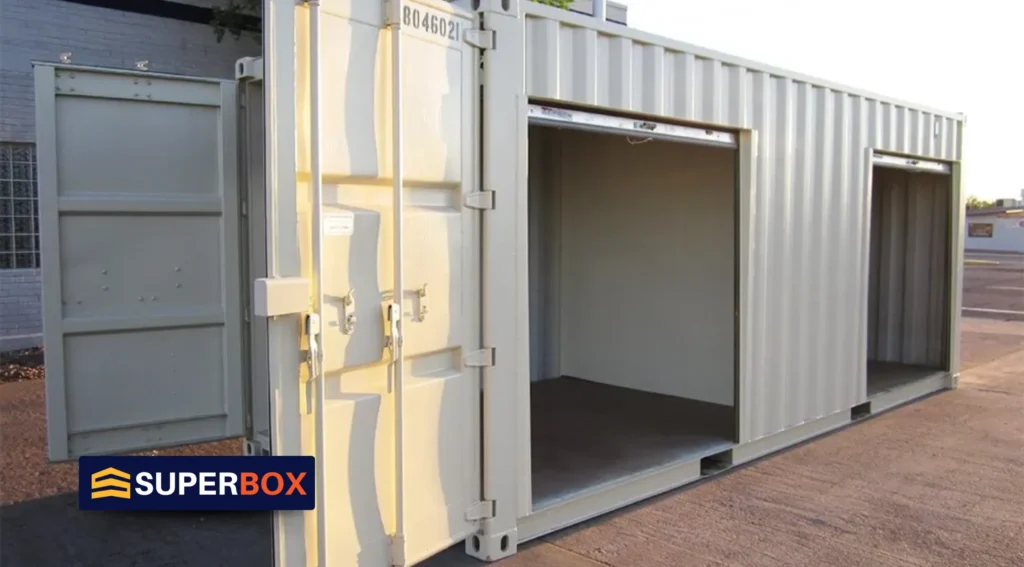
Customization and Modification: Tailoring Containers for Specific Needs
Shipping containers are not just used for transporting goods; they can also be customized and modified for various purposes. The customization process begins with selecting the right type of container for the intended use. Standard containers can be modified to include additional doors, windows, ventilation systems, and insulation.
The modification process typically involves cutting openings in the container’s steel walls and reinforcing them to maintain structural integrity. For example, if a container is being converted into a mobile office, windows and doors may be added, along with electrical wiring and insulation to make the space comfortable.
Containers can also be customized for specialized storage, such as temperature-controlled environments for perishable goods. In these cases, refrigeration units and thermal insulation are installed to maintain the required temperature.
The possibilities for customization are endless, making shipping containers a versatile option for various applications beyond transportation.
Conclusion
The shipping container manufacturing process is a complex and precise operation, involving everything from assembling the steel components to rigorous quality control measures. By understanding this process, you can appreciate the craftsmanship and technology that go into creating these durable and versatile containers. Whether used for transporting goods across the globe or customized for unique purposes, shipping containers are a testament to modern manufacturing techniques and engineering excellence.
Looking for reliable shipping containers? SuperBox has you covered!
Say farewell to shipping challenges with SuperBox’s robust and reliable containers. Whether you run a large enterprise or a small business, our containers are engineered to protect your cargo throughout transit.
Designed for strength and quality, SuperBox containers adhere to the highest standards in modern shipping. For a hassle-free shipping experience, contact us at 1-866-696-9269 to find out how we can offer the perfect container solution for your needs. Our team is here to assist you in ensuring your goods are transported safely and effectively.