Shipping containers are the backbone of global trade, moving goods across oceans and continents. Over the years, technology has dramatically changed how these containers are produced, making the process faster, cheaper, and more efficient. In this blog, we’ll explore the role of robotics and automation in manufacturing shipping containers, the new materials and technologies that could shape their future, and the sustainability initiatives that aim to make container production more environmentally friendly.
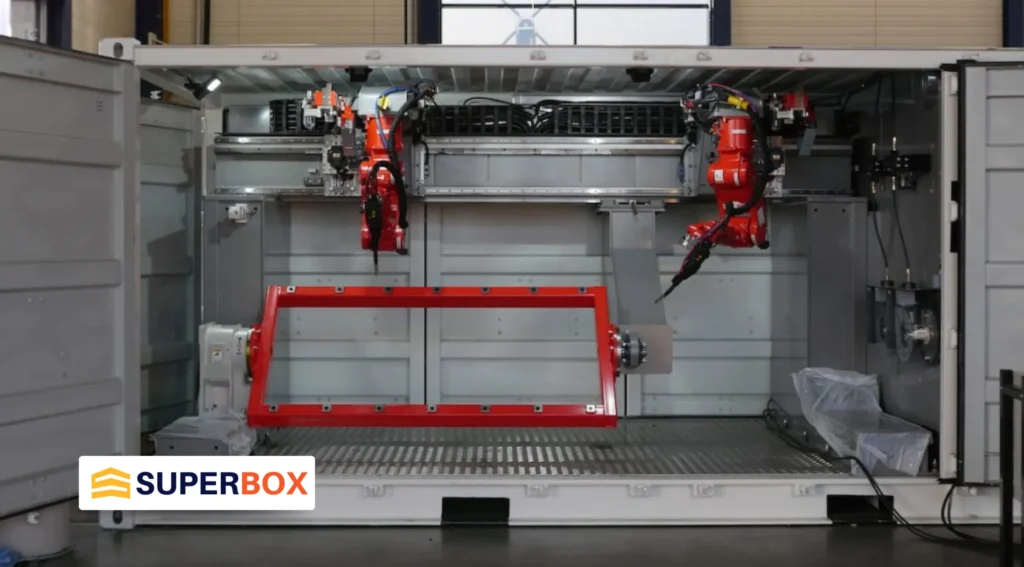
Automated Manufacturing Processes: The Role of Robotics and Automation
1. Robotics in Container Assembly
In the past, shipping container production relied heavily on manual labor. Workers would weld, cut, and assemble the steel components by hand. However, as demand for containers grew, so did the need for faster and more reliable production methods. This is where robotics came into play.
- Welding Robots: Welding is a crucial part of container production. The steel panels that make up the walls, roof, and floor of a container must be securely welded together. Robots now perform most of this work. Welding robots are faster and more precise than human welders, ensuring consistent quality in each container. These robots can work around the clock, significantly boosting production rates.
- Cutting and Shaping: The steel used in shipping containers needs to be cut and shaped before assembly. Automated laser cutters and robotic arms can handle these tasks with high accuracy. They can make precise cuts that reduce material waste and speed up the production process.
- Assembly Line Automation: Modern factories use automated assembly lines where robots move container parts from one station to the next. These robots handle the heavy lifting, positioning large steel panels with precision and ensuring that each piece fits perfectly before welding.
2. Benefits of Automation in Container Manufacturing
Automation in manufacturing has several benefits:
- Increased Efficiency: Robots can work faster than humans and don’t need breaks. This means factories can produce more containers in less time, meeting the growing demand from global trade.
- Consistency and Quality: Automated systems ensure that each container is built to the same high standard. This consistency reduces the chances of defects, which could be costly for shipping companies.
- Safety: Container production involves working with heavy steel and dangerous machinery. By automating these tasks, factories can reduce the risk of accidents and injuries to workers.
- Cost Reduction: While the initial investment in robotics and automation technology can be high, the long-term savings are significant. Automated factories require fewer workers and can produce containers more quickly, lowering overall production costs.
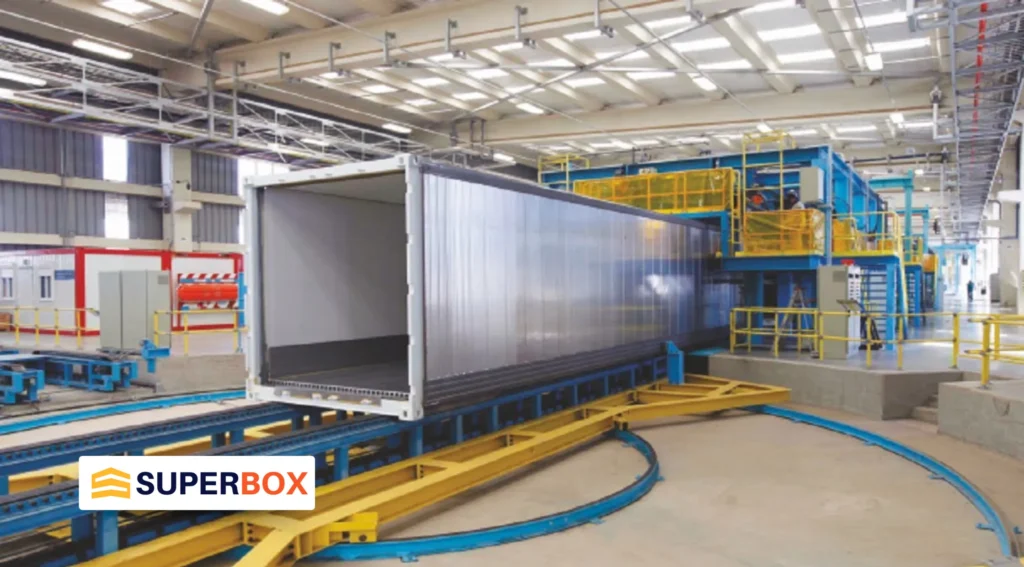
New Materials and Technologies in Shipping Containers
As technology advances, so do the materials and methods used to create shipping containers. Researchers and manufacturers are constantly looking for ways to make containers stronger, lighter, and more durable. Here are some of the latest developments.
1. High-Strength Steel
Traditional shipping containers are made from a type of steel called corten steel, known for its durability and resistance to corrosion. However, new high-strength steel alloys are being developed to improve container performance further.
- Advantages of High-Strength Steel: This new steel is lighter than traditional corten steel but just as strong, if not stronger. Using lighter materials means that containers can carry more cargo without increasing their overall weight, improving fuel efficiency during transport. Additionally, high-strength steel is more resistant to dents and other damage, extending the container’s lifespan.
2. Composite Materials
Another exciting development in container manufacturing is the use of composite materials. These materials are made by combining two or more different substances to create a product with better properties than its components.
- Fiberglass Reinforced Plastic (FRP): One of the most promising composite materials for shipping containers is FRP. This material is strong, lightweight, and resistant to corrosion. Unlike steel, FRP doesn’t rust, making it ideal for containers that will be exposed to harsh weather conditions. FRP containers are also easier to repair if damaged, reducing maintenance costs.
- Carbon Fiber: Carbon fiber is another material that could revolutionize container manufacturing. It’s incredibly strong and lightweight, which could significantly reduce shipping costs. However, carbon fiber is currently expensive to produce, so it’s mainly used in high-value goods containers.
3. Smart Containers
As part of the growing trend toward the Internet of Things (IoT), some companies are developing “smart containers” equipped with sensors and tracking devices.
- Temperature and Humidity Sensors: These sensors monitor the conditions inside the container, ensuring that goods like food, medicine, and electronics are stored at the right temperature and humidity levels. If conditions change, the sensors can alert the shipping company to take action, reducing the risk of spoilage or damage.
- GPS Tracking: Smart containers can also be equipped with GPS devices that allow companies to track their location in real-time. This is particularly useful for high-value shipments, as it provides greater security and helps prevent theft or loss.
- Data Collection: The data collected by these smart containers can be analyzed to improve shipping routes, reduce fuel consumption, and increase overall efficiency in the supply chain.
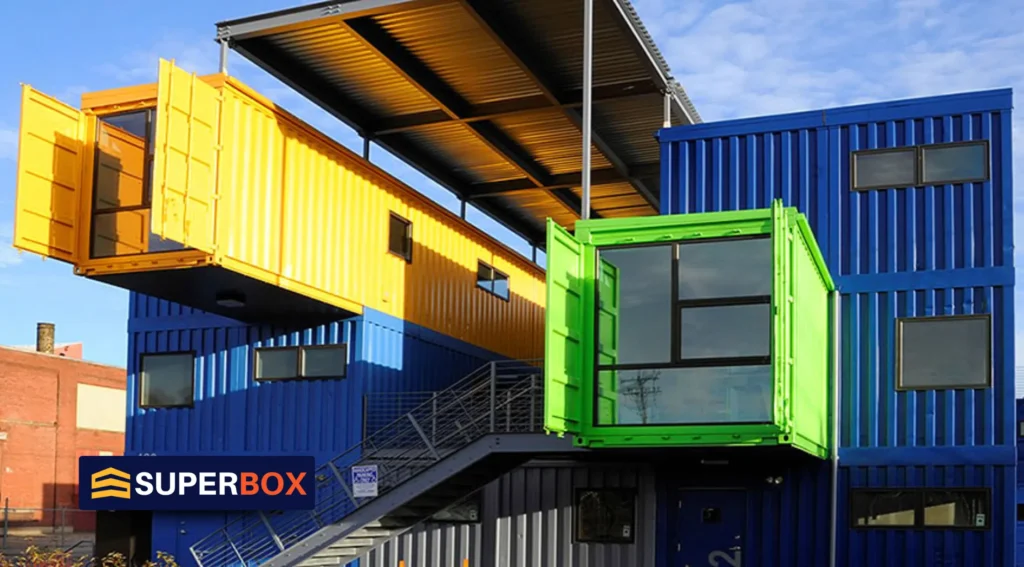
Sustainability Initiatives in Container Manufacturing
The shipping industry is responsible for a significant portion of global greenhouse gas emissions. As concerns about climate change grow, there is increasing pressure to make container manufacturing more sustainable. Here are some of the key initiatives being pursued.
1. Recycling and Reusing Materials
One of the most effective ways to reduce the environmental impact of container manufacturing is to recycle and reuse materials.
- Recycling Steel: Steel is the primary material used in shipping containers, and it can be recycled repeatedly without losing its properties. Many manufacturers are now using recycled steel to produce new containers, reducing the need for raw materials and lowering the carbon footprint of production.
- Upcycling Old Containers: Instead of scrapping old containers, some companies are finding creative ways to repurpose them. For example, old containers can be converted into mobile offices, homes, or storage units. This not only reduces waste but also gives containers a new lease on life.
2. Energy-Efficient Production
Reducing energy consumption during the manufacturing process is another way to make container production more sustainable.
- Solar-Powered Factories: Some container manufacturing facilities are beginning to use renewable energy sources, such as solar power, to run their operations. By relying on solar energy, these factories can reduce their dependence on fossil fuels and lower their carbon emissions.
- Energy-Efficient Machinery: Modern manufacturing equipment is designed to be more energy efficient than older machines. This includes everything from robotic welders to automated cutting tools, which use less power while still delivering high-quality results.
3. Eco-Friendly Coatings and Paints
The paint and coatings used on shipping containers are essential for protecting them from rust and corrosion. However, traditional paints often contain harmful chemicals that can be released into the environment.
- Low-VOC Paints: Manufacturers are now developing low-VOC (volatile organic compound) paints that are less harmful to the environment. These paints release fewer toxic fumes during application and drying, making them safer for workers and reducing air pollution.
- Biodegradable Coatings: Some companies are also experimenting with biodegradable coatings that can be safely absorbed by the environment when a container reaches the end of its life. These coatings provide the same level of protection as traditional ones but with a much smaller environmental impact.
4. Carbon Offsetting and Emission Reduction Programs
In addition to making the manufacturing process greener, some companies are investing in carbon offsetting programs to neutralize their emissions.
- Reforestation Projects: By planting trees or investing in forest conservation, manufacturers can offset the carbon emissions produced during container production. Trees absorb CO2 from the atmosphere, helping to balance out the carbon footprint of manufacturing.
- Emission Reduction Technologies: Some companies are also investing in technologies that reduce emissions at the source. This could include upgrading factory equipment to more energy-efficient models or installing systems that capture and store CO2 before it can be released into the atmosphere.
Conclusion
The future of shipping container manufacturing is being shaped by technology, innovation, and a growing commitment to sustainability. Robotics and automation have revolutionized the production process, making it faster, safer, and more efficient. New materials and technologies promise to create stronger, lighter, and smarter containers. At the same time, sustainability initiatives are helping to reduce the environmental impact of container production, paving the way for a greener future in global trade. As these trends continue to develop, the humble shipping container will remain a vital tool in the global economy, evolving to meet the challenges of the 21st century.
Looking for reliable shipping containers? SuperBox has you covered!
Looking for dependable shipping containers? SuperBox is your solution! Wave goodbye to shipping hassles with SuperBox’s durable and trustworthy containers. Whether you manage a large corporation or a small business, our containers are built to safeguard your cargo during transit. Crafted for strength and quality, SuperBox containers meet the highest standards in today’s shipping industry. For a seamless shipping experience, call us at 1-866-696-9269 to learn how we can provide the ideal container solution for your needs. Our team is ready to help you ensure your goods are transported safely and efficiently.